Spiral Submerged-arc Welded Quality Assurance
Spiral welded pipe production by submerged arc method is based on using tandem welding technique for joining inside and outside coil edges, which have been trimmed and beveled by carbide milling for high quality weld structure.
Excellent Equipment:
There are nine modernized product lines in our company with the yield capacity of 1000 thousands tons of B-X80 steel pipe of φ219-φ3200mm, WT5-30mm.
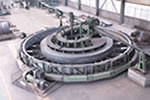
Supercoil Accumulator
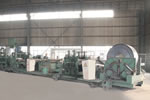
SSAW pipe mills
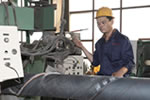
Lincoln Welder Welding
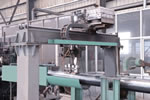
Ultrasonic Inspecting
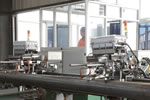
Airport
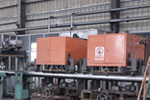
Normalizing
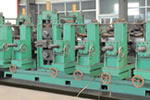
Forming Machine
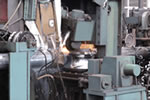
High Frequency Welding
Note:
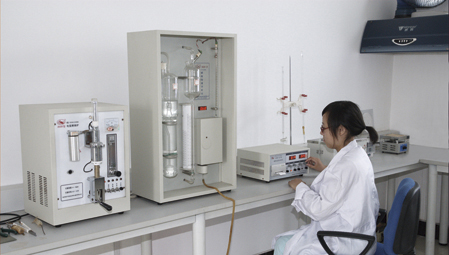
Chemical Analysis
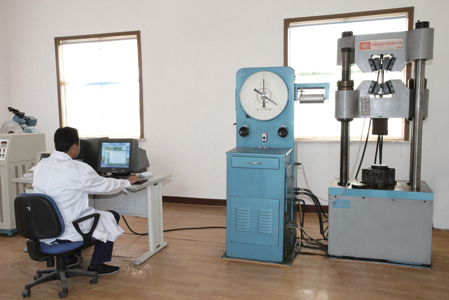
Universal Testing Machine
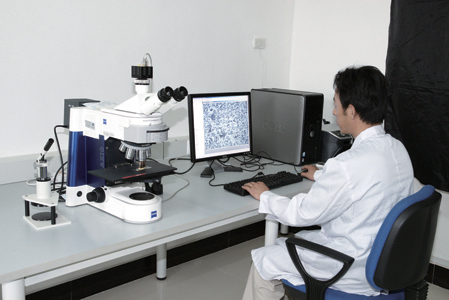
Metallurgical Analysis
Welding of hot rolled steel coils takes spiral form after passing through preforming and forming rolls. Excellent exterior weld quality at high production speeds is provided by double submerged arc welding process. Manufactured pipes are cut to the desired lengths at the exit of the pipe machine. Pipe ends are beveled by means of carbide machining for accurate on-site welding.
After the pipe is conveyed to hydrostatic testing and off-line ultrasonic testing and/or real time X-ray inspection, the pipe will be subject to final inspection for the compliance to customer requirements.
Starting from incoming control up to the final inspection stage; entire process is monitored and supported by computerized system. Traceability is achieved by input controls and barcodes through entire production lines.