Types of Blind Flanges
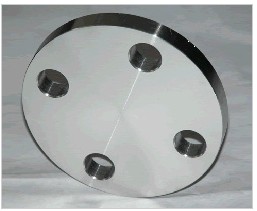
Blind flanges close the ends of pipes. Plumbers have a variety of flanges to choose from when installing pipes in a home. Some of the flanges have greater strength and durability than other flanges, but, with greater durability, usually comes higher costs. Also, some flanges benefit the plumber because the plumber can remove them and recycle them if the pipe fails.
Slip of Flanges
Slip of flanges lack the strength of welding neck flanges under internal pressure. Also, the slip of flanges give out sooner than the welding neck flanges. The pipe must have a thickness greater than 3 mm or else the flange face will break during the welding process. The welder cannot weld the slip of flange with the elbow or the tee because the fittings do not have a straight end.
Welding Neck Flanges
Welding neck flanges have a long tapered hub that the plumber can put over the pipe or fitting. The long tapered hub provides reinforcement in situations of high pressure, low temperatures or very high temperatures. The flange thickness smoothly transitions to pipe thickness when strain or line expansion causes the pipe to bend. The engineers bore the welding neck flanges to match the inside diameter of the mating pipe, preventing turbulence and reducing erosion. This flange also helps distribute stress throughout the pipe.
Lap Joint Flanges
Lap joint flanges do not have raised faces, but otherwise the engineers made these flanges almost identical to the slip of flanges. However, the lap joint flange has a different radius, a radius to allow the entry of the flanged portion of the stub end. Like the slip of flanges, the lap joint flanges cannot hold very much strain though they have somewhat more sturdiness than the slip of flanges. The lap joint flanges can swivel around the pipe so that the welder can line up the opposing flange bolt holes. Also, fluid in the pipe does not touch the flanges, allowing the welder to use cheaper carbon steel flanges. The plumber can also easily salvage the lap joint flanges if the original pipes are broken.
Socket Weld Flanges
Welders primarily use socket weld flanges for small and high-pressure piping. This socket weld flange has greater strength than the slip of flange. When welding the flange, the welder must create a space between the flange and the pipe. By providing bottoming clearance of the socket weld, the residual stress of the root of the weld falls because of the solidification of the weld metal. However, the separation creates a crack that can cause corrosion problems for both the pipe and the flange.