Casing and Tubing
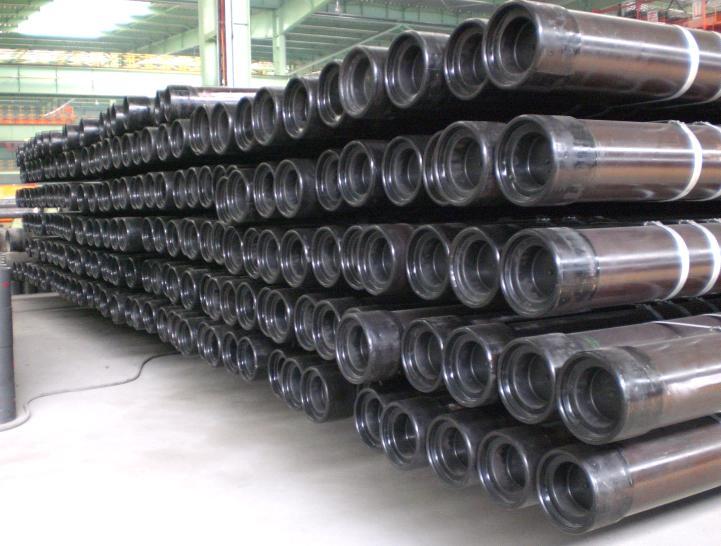
Oil country tubular goods (OCTG) is a family of seamless rolled products consisting of drill pipe, casing and tubing subjected to loading conditions according to their specific application.
Standards:
- API Spec 5CT latest edition at time of manufacture (PSL-1, PSL-2, PSL, 3)
- ISO 11960:2004, Petroleum and natural gas industries-Steel pipes for use as casing or tubing for wells
Sizes range:
- Outside Diameter: 1.660″ – 30″
- Length:Range 1, Range 2 & Range 3
Casing Thread
- Available in short thread and coupling (S.T.C)
- long thread and coupling (L.T.C)
- buttress threaded and coupled (B.T.C)
Grades:
- Casing H40, J55-K55, N80, L80 (1), C95, P110
- Tubing H40, J55-K55, N80, L80 (1), C95, P110
- Drill Pipes E75, X95, G105, S135
Connections:
- STC (short round thread casing)
- LTC (long round thread casing)
- BTC (buttress thread casing)
- XL (extreme-line casing)
- NUE (non-upset tubing)
- EUE (external upset tubing)
- IJ (integral joint tubing)
Corrosion resistance under sour service conditions is a very important OCTG characteristic, especially for casing and tubing.Tubing is pipe through which the oil or gas is transported from the wellbore.
Tubing segments are generally around 30 ft [9 m] long with a threaded connection on each end. |
Premium Connections
And almost any premium & gas tight connection
Protection:
- External bare and uncoated or externally coated with black/ transparent anti rust Mill varnish
- Plastic or Metal Pin and Box Protectors.
- Internal plastic coating or sleeves.
Mill Test Certificates:
- Issued in accordance with API Specification 5CT Eighth Edition
- Additional Third Party Inspection can also be performed on request.
For pipes covered by this standard, the sizes, masses and wall thicknesses as well as grades and applicable end-finishes are listed in Tables C.1 to C.3 and Tables E.1 to E.3. By agreement between the purchaser and manufacturer, this standard can also be applied to other plain-end pipe sizes and wall thicknesses.
The main chemical compositions(%) of Tubing and Casing:
Grade | Type | C | Mn | Mo | Cr | Ni | Co | P | S | Si | ||||
Min | Max | Min | Max | Min | Max | Min | Max | Max | Max | Max | Max | Max | ||
H40 | - | - | - | - | - | - | - | - | - | - | - | 0.03 | 0.03 | - |
J55 | - | - | - | - | - | - | - | - | - | - | - | 0.03 | 0.03 | - |
K55 | - | - | - | - | - | - | - | - | - | - | - | 0.03 | 0.03 | - |
N80 | 1.00 | - | - | - | - | - | - | - | - | - | - | 0.03 | 0.03 | - |
N80 | Q | - | - | - | - | - | - | - | - | - | - | 0.03 | 0.03 | - |
M65 | - | - | - | - | - | - | - | - | - | - | - | 0.03 | 0.03 | - |
L80 | 1.00 | - | 0.43a | - | 1.90 | - | - | - | - | 0.25 | 0.35 | 0.03 | 0.03 | 0.45 |
L80 | 9Cr | - | 0.15 | 0.30 | 0.60 | 0.90 | 1.10 | 8.00 | 10.00 | 0.50 | 0.25 | 0.02 | 0.01 | 1.00 |
L80 | 13Cr | - | 0.22 | 0.25 | 1.00 | - | 12.00 | 14.00 | 0.50 | 0.25 | 0.02 | 0.01 | 1.00 | |
C90 | 1.00 | - | 0.35 | - | 1.20 | 0.25b | 0.85 | - | 1.50 | 0.99 | - | 0.02 | 0.01 | - |
C90 | 2.00 | - | 0.50 | - | 1.90 | - | Nl | - | NL | 0.99 | - | 0.03 | 0.01 | - |
C95 | - | 0.45c | - | 1.90 | - | - | - | - | - | - | 0.03 | 0.03 | 0.45 | |
T95 | 1.00 | - | 0.35 | - | 1.20 | 0.25d | 0.85 | 0.40 | 1.50 | 0.99 | - | 0.02 | 0.01 | - |
T95 | 2.00 | - | 0.50 | - | 1.90 | - | - | - | - | 0.99 | - | 0.03 | 0.01 | - |
P110 | - | - | - | - | - | - | - | - | - | 0.03 | 0.03 | - | ||
Q125 | 1.00 | - | 0.35 | - | 1.00 | 0.75 | - | 1.20 | - | 0.99 | - | 0.02 | 0.01 | - |
Q125 | 2.00 | - | 0.35 | - | 1.00 | NL | - | NL | - | 0.99 | - | 0.02 | 0.02 | - |
Q125 | 3.00 | - | 0.50 | - | 1.90 | NL | - | NL | - | 0.99 | - | 0.03 | 0.01 | - |
Q125 | 4.00 | - | 0.50 | - | 1.90 | NL | - | NL | - | 0.99 | - | 0.03 | 0.02 | - |
Note:
a product uses oil quenching, L80 grade carbon content of the upper limit may be increased to 0.50%.
b If the wall thickness
c If the product oil quenching, the C95 grade carbon content limit may be increased to 0.55%.
d If the wall thickness
NL-Not limit, but must show the element content in the product by reported.
Mechanical Properties of Tubing and Casing
Grade | Type | TEUL(%) | Yield strength (Pa) |
Tensile (MPa) |
Hardnessa | S.W.T. (m) |
HRCb | ||
Min | Max | Min | Min | Max | |||||
H40 | - | 0.5 | 276 | 552 | 414 | - | - | - | - |
J55 | - | 0.5 | 379 | 552 | 517 | - | - | - | - |
K55 | - | 0.5 | 379 | 552 | 655 | - | - | - | - |
N80 | 1 | 0.5 | 552 | 758 | 689 | - | - | - | - |
N80 | Q | 0.5 | 552 | 758 | 689 | - | - | - | - |
M65 | - | 0.5 | 448 | 586 | 586 | 22 | 235 | - | - |
L80 | 1 | 0.5 | 552 | 655 | 655 | 23 | 241 | - | - |
L80 | 9Cr | 0.5 | 552 | 655 | 655 | 23 | 241 | - | - |
L80 | 13Cr | 0.5 | 552 | 655 | 655 | 23 | 241 | - | - |
C90 | 1,2 | 0.5 | 621 | 724 | 689 | 25.4 | 255 | 鈮12.70 | 3 |
C90 | 1,2 | 0.5 | 621 | 724 | 689 | 25.4 | 255 | 12.71~19.04 | 4 |
C90 | 1,2 | 0.5 | 621 | 724 | 689 | 25.4 | 255 | 19.05~25.39 | 5 |
C90 | 1,2 | 0.5 | 621 | 724 | 689 | 25.4 | 255 | 25.4 | 6 |
C95 | - | 0.5 | 655 | 758 | 724 | - | - | - | |
T95 | 1,2 | 0.5 | 655 | 758 | 724 | 25.4 | 255 | 12.70 | 3 |
T95 | 1,2 | 0.5 | 655 | 758 | 724 | 25.4 | 255 | 12.71~19.04 | 4 |
T95 | 1,2 | 0.5 | 655 | 758 | 724 | 25.4 | 255 | 19.05~25.39 | 5 |
T95 | 1,2 | 0.5 | 655 | 758 | 724 | 25.4 | 255 | 25.4 | 6 |
P110 | - | 0.6 | 758 | 965 | 862 | - | - | - | - |
Q125 | 1~4 | 0.65 | 862 | 1034 | 931 | b | - | 12.70 | 3 |
Q125 | 1~4 | 0.65 | 862 | 1034 | 931 | b | - | 12.71~19.04 | 4 |
Q125 | 1~4 | 0.65 | 862 | 1034 | 931 | b | - | >=19.05 | 5 |
Note:
a Dispute, the Rockwell hardness of the laboratory should be used as the arbitration.
b Hardness limit is not specified, but according to the provisions of 7.8 and 7.9 in the most amount of change as production control.
TEUL: Total elongation under load
SWT: Specified wall thickness
HRC Allowable hardness change